A rotary valve or an airlock feeder is a bulk material handling equipment used to modulate the flow of dry bulk solids from upstream equipment such as storage silos, hoppers and dust collection systems to downstream systems like pneumatic conveying systems, belt conveyors, and screw feeders. Polimak is an industrial company concerned with the design and production of various machinery used for handling dry bulk materials. With over four decades of experience in the bulk solids industry, our objective is to devise and produce cutting-edge bulk solids machinery that provide quality performance during bulk material handling for our clients.
Rotary valves are referred to by various names, with the term airlock valves being the commonly used one. Its primary function is to regulate bulk material flow from one piece of equipment to another and maintain a constant air pressure between the two ports of the valve (inlet and outlet). This is attained with the help of the rotor blades. Airlock valves are a fundamental component in bulk handling systems. They are widely used in many different industries such as food, chemical, plastics, cement, agriculture and many others for various bulk material handling processes.
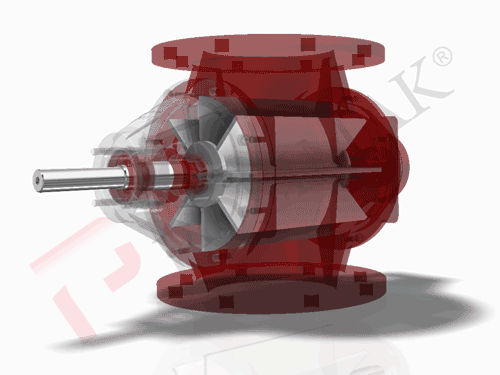
Rotary Valves Features
Polimak offers various valve configurations depending on the characteristics of the handled bulk materials and the application, respectively. The rotary valve production obeys general practical engineering precision. The fundamental valve components include a valve body (housing) with an inlet port and an outlet port, a rotor (shaft with blades), two end plates (outboard or inboard) and a drive system.
Housing
A rotary valve housing secures the bulk material flowing through it by containing it throughout the material handling. Our housings are produced from several materials of construction such as cast iron, stainless steel and hardox. We render special coatings for abrasive bulk materials as well as highly polished finishes for the food and dairy industries. The three housing configuration types present are flow through, blow through and offset.
Rotors
Rotors function as metering components in rotary valves. These components differ in design from each other. A rotor is also known as a rotor assembly since it is made up of a shaft and blades (also known as vanes) that are welded or cast together. It is the valve’s rotating component. Different rotors have different numbers of rotor vanes; 6, 8 and so on. The space between the vanes is known as a rotor pocket. The lower the number of rotor pockets the higher the pocket capacity.
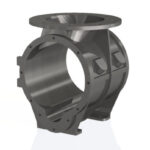
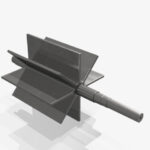
End-plates
The rotary valve end-plates make sure that the bulk materials don’t spill off on the side of rotor pockets. There are two configuration types of end-plates namely outboard and inboard bearing end-plates. Bearings on outboard plates are moved away from the head plates and are typically used in heavy-duty rotary valve models. These plates contain seals in them. The primary purpose of the seals is to prevent dry bulk material outflow from rotor pockets to the bearing region. Lip seals or gland packing can be used.
Drive Systems
The motor and the gearbox combine to form what is known as the valve’s drive system. Most of the rotary valves are driven through a reduction gearbox that is powered by an electrically induced motor. The reduction gearbox is normally utilized to receive a specific motor speed and produce a low output speed. The three drive arrangements that Polimak offers are; a worm gear reduction connection, a chain gear connection and a direct coupling connection.
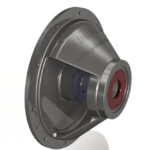
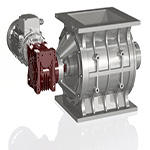
Bulk Materials Handled by Rotary Valves
A rotary valve is designed according to the dry bulk materials which it is processing. Different types of dry bulk solids demand different valve designs. Coated surfaces that are non-stick or polished stainless-steel surfaces are commonly used for products having corrosive, sticky, and cohesive characteristics.
Some of the bulk materials that can be handled using a rotary valve are sugar, salt, spices, wheat, rice, cornstarch, corn (maize), bran, coffee beans, broad beans, milk powder, coffee powder, wheat flour, cornstarch, plastic pellets, rubber powder, cement, fly ash, sand, alumina, copper oxide, sodium sulphate, calcium carbonate, limestone etc.
Rotary Valves FAQ
What is a rotary valve?
A rotary valve is a compact mechanical device broadly used in dry bulk materials handling applications to control the flow of dry bulk solids between two systems, upstream and downstream equipment. It is known by a variety of names, airlock valve, star valve, rotary feeder etc.
What is the difference between a rotary feeder and an airlock feeder?
A rotary feeder a valve whose primary function is to feed or meter dry bulk solids from an upstream device to a downstream device without necessarily separating a pressure differential. An airlock feeder on the other hand is a valve that separates a pressure differential while feeding or metering dry bulk materials into a downstream system.
How does a rotary valve work?
The blades of a rotary valve rotate inside the valves housing during operation. This rotation is driven by a motor. As the motor rotates, rotor pockets follow through. Dry bulk solids are supplied to the valve from upstream equipment through its inlet and settle in the pocket. The rotor continues to rotate and then discharges the dry bulk solids through its outlet port. Two types of rotation exist; load side rotation and return side rotation. The former is defined as the rotation of the rotor pockets from the inlet to the outlet, whereas the latter is the rotation of the rotor pockets from the outlet port to the inlet port.
Why are rotary valves used?
Rotary valves are used in several industries for various industrial applications. It is used for several different reasons including; the control of dry bulk solids flows, feeding downstream systems, and maintaining a pressure differential between an upstream device and a downstream device.