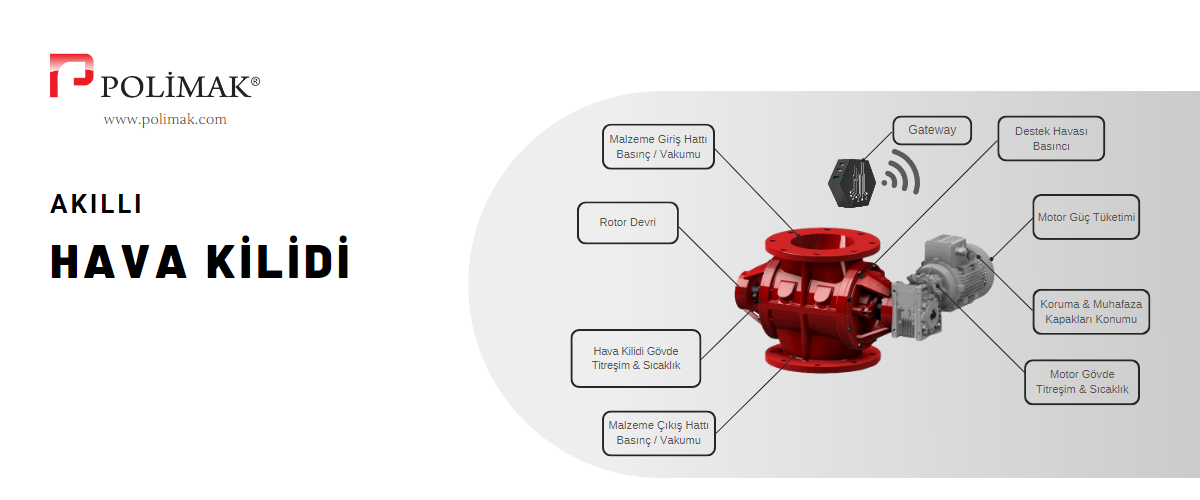
Çimento, tarım, gıda, kimya, plastik gibi proses ve imalat endüstrileri, verimli ve etkili dökme malzeme akışını sağlamak için hava kilitlerini kullanmaktadır. Sürekli ve kesintisiz dökme malzeme akışını sağlamak sorunsuz operasyonlar gerektirir, ancak operasyonel sorunlar yaşanabilir. Bu sorunlar arasında anormal titreşimlere neden olan rotor şaftının yanlış hizalanması, ısı birikiminin neden olduğu rulman hasarı, conta bozulmasına yol açan hava tahliye arızaları, beklenenden daha yüksek dökme malzeme sıcaklığının neden olduğu rotor genleşmesi nedeniyle gürültülü işlemler ve biriken dökme katıların neden olduğu sıkışma, besleyicinin titremesine neden olarak sonunda tahrik zincirinin kaymasına veya rotor hızının etkilenmesine neden olması sayılabilir. Ayrıca, iki bağlantı noktasındaki (giriş ve çıkış) aşırı hava kaçağı nedeniyle yetersiz malzeme çıkışı da bu temel ekipmanlar için yaygın bir sorundur. Çoğu sektörde manuel makine kontrolleri, yukarıda bahsedilen operasyonel sorunların zamanında tespit edilmesini zorlaştırabilir. Bu durum, üretim performansında kayıplara ve makinelerin uzun ömürlülüğü üzerinde planlanmamış arıza süresi maliyetleri, artan bakım ücretleri, performans sağlığının azalması ve ekipman ömrünün kısalması gibi ciddi sonuçlar doğurabilir.
Endüstri 4.0’ın otomasyon ve diğer önemli IIoT – Endüstriyel Nesnelerin İnterneti teknolojileri aracılığıyla operasyonel verimliliği artırmasıyla Polimak, proses ve imalat endüstrilerinin üretim hatlarındaki plansız çalışma/bakım sürelerini azaltmasına yardımcı olan son teknoloji akıllı döner besleyiciler (hava kilitleri) sunmak için endüstri 4.0’ın ve konseptlerinin gücünden yararlanıyor. Polimak, akıllı hava kilitleri sunmak için üretim ve proses endüstrisindeki bilgi birikimini yazılım teknolojisindeki uzmanlığıyla birleştiriyor. Polimak akıllı hava kilidi (genellikle proses hatlarında bir dökme malzeme taşıma/boşaltma sistemi altında kullanılır ve iki ekipman grubu arasındaki dökme malzeme akışını verimli bir şekilde düzenler); proses koşullandırma, makine sağlığı ve envanter izleme ve bilgisayar destekli bakım yönetimi teknolojilerini birleştiren IoT çözüm platformumuza (Politrace) entegre edilmiştir. Ekipman, döner besleyici (hava kilidi) gövdesinin sıcaklığı ve titreşimi, hem giriş hem de çıkış portlarında hava basıncı ölçümleri, rotor hızı, yatak sıcaklığı, güç tüketimi, hava tahliyelerindeki hava basıncı ve besleyici çalışırken güvenlik koruyucu kapak algılama dahil olmak üzere çeşitli operasyonel ünite parametrelerinin sürekli olarak izlenmesini sağlayan bir sensör sistemi ile donatılmıştır. Sensör sistemi, hava kilidi performansını ve durumunu derinlemesine izleme imkanı sunarken, kapsamlı gerçek zamanlı veriler toplar. Bu veri toplama süreci, cihaz çalışırken herhangi bir anormallik ortaya çıkarsa erken tespit uyarısı sağlar; bu da personele düzeltici eylemde bulunmak için yeterli zaman vererek maliyetli arızaların ortaya çıkmadan önlenmesine yardımcı olur. Polimak akıllı hava kilitlerinin faydaları arasında aşağıdakiler yer almaktadır:
- Ekipmanın beklenmedik arıza sürelerinde azalma.
- Yüksek dökme malzeme taşıma/boşaltma kapasitesi.
- Minimuma indirilmiş bakım maliyetleri.
- Üretim hattı performansında iyileşme.
- Gerçek zamanlı verilerin gözlemlenmesi.
- Öngörülebilir bakım.
- Tüm anormal değerler için bildirim uyarısı
Polimak’ın IoT – Nesnelerin İnterneti çözümünün uyumluluğu sadece hava kilitleriyle sınırlı kalmayıp, proses hatları boyunca çeşitli ekipmanlara entegre edilebilmektedir. Üretim sistemlerinin/ekipmanlarının IoT çözümümüzle birlikte çalışması, verileri gerçek zamanlı olarak gönderen sistemler/ekipmanlar yaratır.