Train transportation is one of the most convenient transportation methods, as it is cost-effective. But the train size difference does not allow one train to move across the whole of Europe. There are several options to solve this problem considering the carried product type.
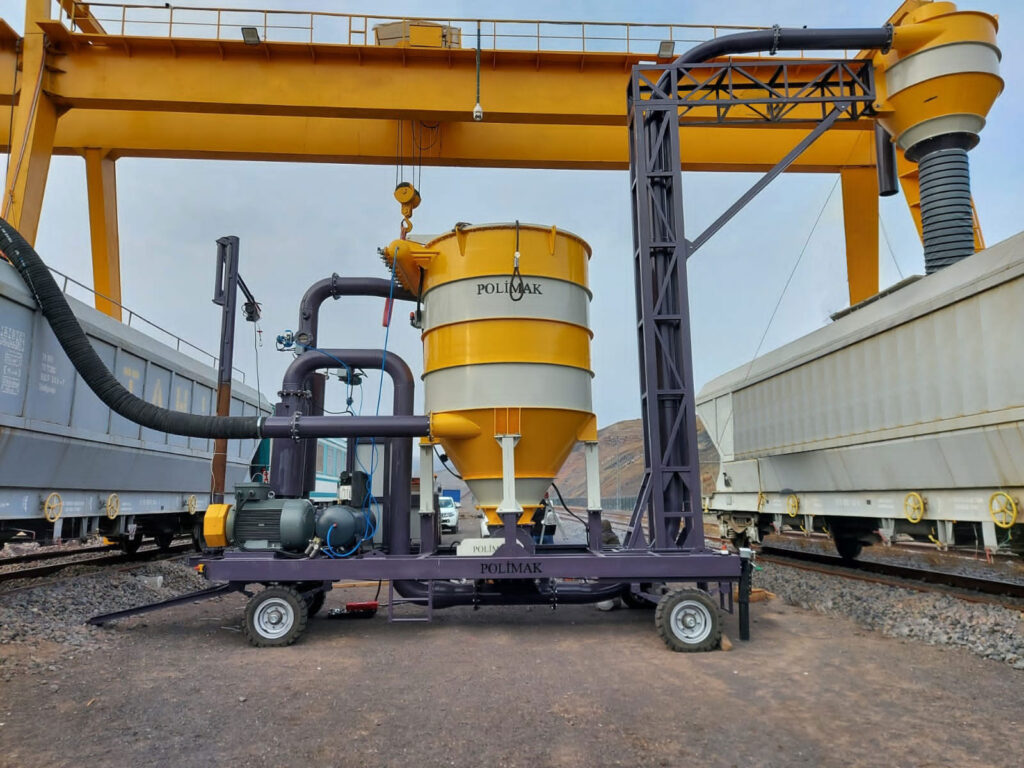
Different Train Gauges of Europe
Being used since the 19th century, rail transportation has never lost its popularity. But Europe has a wide variety of train gauges, which creates logistical problems. A train cannot simply move from one country to another because of the rail gauge size differences. Before the International Union of Railways (IUC) was founded and determined a standard gauge width, countries were determining train gauge standards considering some factors. For example, post-Soviet bloc countries such as Latvia, Lithuania, Moldova, and Ukraine, have Russian train gauge. Scandinavian countries like Switzerland adapted their trailway considering their topography with tight curved mountains, so they use shorter gauge. Although IUC determined a standard gauge width, the networks that are already set were not revised. Train transportation is an easy and cost-effective land transportation method for importing and exporting, but the rail gauges difference creates a serious transportation problem.
Depending on the transported material type, solutions such as carrying a wagon from one rail to another, using adaptable wagon wheels that can move on different rail gauges or unloading contents of one wagon and loading them to the next one at each border crossing is preferred. Transferring bulk solids (such as grains, coal, various ores like iron, fertilizers, sugar) in powdered or granular form can be a messy, and dusty, time-consuming process. Polimak Group has been providing bulk solid handling systems for over 40 years and we aim to handle dust-free, fast, and efficient solutions especially for pneumatic conveying of bulk solids.
Polimak Bulk Solid Mobile Wagon Unloader
Our design offers a practical transfer of bulk materials between one wagon to another wagon or a truck. The working principle is based on using a blower and a pneumatic conveying line. Procedure starts with unloading the bulk material by suctioning, with suction air supplied from the blower. Then the product is separated from suction air inside the jet cyclone, and fed to the pressurized conveying line with the rotary valve placed below the jet cyclone. Lastly, the bulk material is conveyed to the next system with pressurized air, again provided by the same blower. This Polimak system is designed to be compact, such that it can fit in a container and is easy to install. The wheeled chassis carrying the whole system enables maneuverability so transferring goods can be made just by moving the system, instead of moving the entire train.